Our company started manufacturing and supplying cryogenic air separation plants in 1997. Soon after BDM started creating the buzz by dint of its immaculately conceived liquid oxygen plant and fabricated with materials with fully complying with ASME code. Our visionary leadership realized early on that the quickest, surest and the steadiest path into the mind of customers goes through the business practices called trust, product quality, efficient pricing and amazing customer service.
We have high level of expertise in the designing, designing and fabrication. And, we have efficient channels and supply chain for providing spare parts for customers using LOX plants, which have a life-cycle of over 25 years. During the long life of the plant machinery, the customers will have assured access to the spare parts. And, we also provide world-class after sales service. Though the plant machinery requires minimum maintenance and seldom requires change of spare parts. When you need the spare parts it would be easily available through our supply chains.
Designing of the liquid oxygen manufacturing plant is accomplished our experts having years of preparing innovative designs. Many of our designers have worked at reputed European air separation plant manufacturers and have got invaluable experience. Manufacturing is done with high quality materials which comply with ASME code. Globally accepted manufacturing practices and standards are complied with. All components used in the making of the machinery are sourced only from the best OEMS. We use cryogenic grade materials which can endure the wear and tear of extreme temperature and pressure. We are one of the few LOX plant manufacturing companies that use argon welding.
Basic Principle :
Better Deal Machinery manufactures liquid oxygen generator plant with technology based on cryogenic air separation. This process takes in the abundantly available atmospheric air which is then compressed and filtered in the air compressor of the plant. Then it is cleaned in the purification unit from impurities such as carbon dioxide, hydrocarbon and moisture. Now, the air is passed through a series of heat exchangers where it is liquefied at cryogenic temperatures. Afterwards it is sent into a high pressure distillation column where it is separated into constituent elements—oxygen and nitrogen. Next the chosen gas is sent into the low pressure distillation column distilling it to commercially required purity.
Competitive Advantages :
- Efficient and precision designing
- ASME quality materials
- Low pressure technology
- High purity oxygen
- Skid mounted needing no foundation
- Air separation column fabricated with high grade stainless steel
- Low energy requirement
- Life cycle of over 25 years
- Low maintenance
- Low operational cost
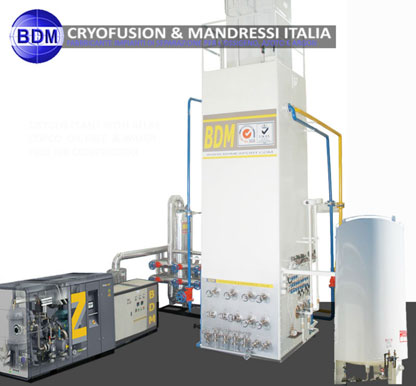
Scope & Supply of Liquid Oxygen Factory
Air Compressor : The best quality air compressor is used in the making. We use oil-free rotary type Atlas Copco air compressors. It uses screw/centrifugal technology compressing air at a low pressure of 5-7 bar (0.5-0.7mpa).
Pre-Cooling System : The process air is pre-cooled with the help of refrigeration to a temperature around 12 degrees Celsius. Then it is moved into the air purifier.
Purification of Air by Purifier : It is also very essential and crucial component of the LOX plants. It is made up of twin molecular sieves made of the highest quality. The process air is cleaned here of impurities including carbon dioxide and moisture. After being purified the air reaches air separation unit.
Cryogenic Cooling of Air by Expander : It is used for liquefying the air which happens at sub-zero temperatures. Liquefaction is achieved at sub-zero temperatures. This refrigeration and sub-zero temperatures can only be achieved using a turbo expander, which cools the air to temperatures below -165 to-170 deg C.
Separation of Air with Air separation Column : The process air is separated into constituent gases—oxygen and nitrogen. Then, the air entering low pressure plate fin type heat exchanger is fully purified which is cooled inside the heat exchanger below sub zero temperatures by air expansion process in the expander. It is imperative that we achieve a difference delta as low as 2 degree Celsius at the warm ends of the exchangers. The process is liquefied when it reaches the air separation column which is separated into oxygen and nitrogen through the process of rectification.
Storage in Liquid Oxygen Tank : Liquid oxygen is stored in liquid storage tank which connected to the liquefier which makes up an automatic system. Liquid oxygen is taken out using a hose pipe.
Industry Benefits
Liquid oxygen is the more preferred choice of the customers because it is the convenient to store and transport. And it is also economical as it is less prone to leakages compared to the gaseous oxygen.
The ideal size of a liquid oxygen production plant is the one that meets the requirements of a customer. We customize the fabrication of the plant as per the requirements of the client.
Yes, cryogenic liquid oxygen plant is provided with a liquid oxygen pump that converts liquid oxygen into oxygen in gas form at a pressure of 150 bar or high as per the requirement.
Yes, liquid oxygen making plant using cryogenic distillation can generate liquid nitrogen as well. However, you will have to buy liquid nitrogen pump for cylinder filling at a pressure of 150 bar or as may be required.
MODEL | LIQUID OXYGEN CAPACITY | PURITY OF OXYGEN | |
---|---|---|---|
BDM L-50 | 55 Liters / hr | 1.5 Tons per day | 99.7% |
BDM L-80 | 90 Liters / hr | 2.5 Tons per day | 99.7% |
BDM L-100 | 100 Liters / hr | 3 Tons per day | 99.7% |
BDM L-150 | 180 Liters / hr | 5 Tons per day | 99.7% |
BDM L-200 | 215 Liters / hr | 6 Tons per day | 99.7% |
BDM L-250 | 290 Liters / hr | 8 Tons per day | 99.7% |
BDM L-300 | 360 Liters / hr | 10 Tons per day | 99.7% |
BDM L-400 | 425 Liters / hr | 12 Tons per day | 99.7% |
BDM L-500 | 540 Liters / hr | 15 Tons per day | 99.7% |
BDM L-1000 | 1170 Liters / hr | 30 Tons per day | 99.7% |
BDM L-1500 | 1755 Liters / hr | 45 Tons per day | 99.7% |
BDM L-2000 | 2340 Liters / hr | 60 Tons per day | 99.7% |
BDM L-3000 | 3515 Liters / hr | 90 Tons per day | 99.7% |
BDM L-4000 | 4685 Liters / hr | 120 Tons per day | 99.7% |
BDM L-5000 | 5850 Liters / hr | 150 Tons per day | 99.7% |
NOTE : THE SAME PLANT CAN ALSO PRODUCE LIQUID NITROGEN ALONG WITH 99.9% PURITY.