We are leaders in making world-class liquid nitrogen plant and other air separation products with features and performance that are at par with the best. Cryogenic air separation technology is used in our manufacturing of the liquid nitrogen generator plant. This process was developed in 1930s by Linde & Claude and is still being used all over the globe for generation of high purity nitrogen. The technique is efficient and has been modified with newer developments in the field of cryogenic technology.
Quality of LIN plants and other products is very important for us. It is important for us that our clients get to experience the superior working of our air separation products. This is ensured by world-class designing and fabrication with the highest quality materials. All the materials used in the making meet the ASME quality standards. Our designing is benchmarked against the best international standards. This helps our plant machinery to deliver reliable and efficient performance.
Good Manufacturing Practices (GMP) is employed at the BDM air separation testing centre at our sprawling factory located in Delhi NCR. To illustrate, we use high grade stainless steel in the making of the air separation column. The materials must have the ability to withstand the disintegrating effects of extreme temperature and pressure. Construction of the plant with inferior quality materials would not sustain the working pressure and yield in to the disintegration. So we use only the best quality materials backed up by highly efficient processes and globally recognized components such as Atlas Copco air compressor.
Basic Principle :
Liquid nitrogen (LIN) plant uses cryogenic distillation process which takes air from the atmosphere and filters and compresses in the air compressor. Afterwards, the process air is moved into a cleanup system for removal of impurities. In order to achieve liquefaction the air goes through a series of heat exchangers cooling the air to cryogenic temperatures. Now the air is passed through a high pressure distillation column separating it into oxygen and nitrogen. Nitrogen is collected and moved into a low pressure distillation column for achieving commercially specified purity.
Salient Features :
- Globally approved quality
- Low investment
- Compact designing
- ASME quality materials
- Cryogenic grade stainless steel fabricated air separation column
- Quicker return on investment
- Low pressure technology
- Low maintenance
- Low operational cost
- High purity nitrogen
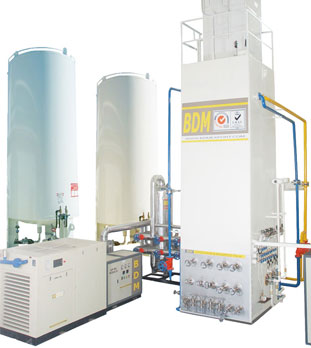
Technical Specifications
Capacity Range : 20liter/hr to 1000liter/hr
Purity : Nitrogen with purity up to 99.99%
Air separation column : Cryogenic grade stainless steel
Technology : Internationally validated cryogenic process
Radiography : 100% in-house radiography of all weld joints and seams
Welding type : TIG argon welding
Scope & Supply of Liquid Nitrogen Plant
Main Air Separation Column : It is said to be the most important part of the cryogenic liquid nitrogen plant since the entire efficiency of the machinery depends on it. Naturally it forms around 60% of the cost of the LN2 plant. It separates the air into oxygen and nitrogen by liquefaction and rectification of air at minus (-) 190 degree Celsius by virtue of difference in the boiling points of Oxygen and Nitrogen. The material of construction should be non-corrosive nonreactive cryogenic grade stainless steel and have qualities such as high tensile strength at cryogenic temperatures to avoid brittle fractures and should not warm quickly (thermal insulation) so it may retain the cold energy for longer time.
Air Compressor : It is a very important component of the liquid nitrogen plant. It is main machinery used for filtering and compressing atmospheric air feeding the plant. It is said to consume around 90% of electric power in oxygen production. Quality of compressed air is very important so we use only the best quality air compressor. It offers comprehensive trouble-free solution.
Process Purification Unit (Skid Mounted) : All the parts of the purification unit are mounted on a single frame skid with each unit complete with piping so that it is ready for installation. Equipment used in the unit responsible for cleansing impurities of the compressed air stream such as hydrocarbons, carbon dioxide, water vapor and dust is maintained at temperature of around 10 degree Celsius using a pre-cooling system.
Nitrogen Cylinder Filling System : It is a very handy process of the liquid nitrogen production plant which is very reliable and efficient due to the built-in liquid nitrogen pump system greatly decreasing the consumption of electricity. It allows the users to fill nitrogen into the cylinders at high pressure.
Start up Time of the Plant : It is imperative that the plant has got a quicker start time. Achieving faster startup is crucial in case of electrical power cut, short stop, restart or overnight stops. However, startup takes time as the plant machinery has to clack temperatures of -190 degrees below zero.
Industry Benefits
PSA technology is based on the process of adsorption where as cryogenic plant function on the liquefaction of atmospheric air & its separation into oxygen and nitrogen based on their boiling points.
Nitrogen plant setup cost depends on the size of the plant and components used inside the machinery. Our plants are offered in the size ranging from 20m3/hr to 1000m3/hr.
Yes, liquid nitrogen plant is better than a concentrator because it is easier to store, transport and not prone to leakages. Moreover, it has higher purity compared to oxygen found in the concentrator.
Liquid nitrogen is stored in the cryogenic liquid nitrogen storage tank which is well-insulated so heat from the surroundings is not able to reach inside the tank.
Liquid nitrogen mainly use of steel & metal manufacturing, food & beverage industry, glass industry, electronics Industry, chemical industry, oil & gas industry, cryopreservation of biological samples including semen, tissues & blood and many more industry.
MODEL | LIQUID OXYGEN CAPACITY | PURITY OF OXYGEN | |
---|---|---|---|
BDM L-50 | 55 Liters / hr | 1.5 Tons per day | 99.7% |
BDM L-80 | 90 Liters / hr | 2.5 Tons per day | 99.7% |
BDM L-100 | 100 Liters / hr | 3 Tons per day | 99.7% |
BDM L-150 | 180 Liters / hr | 5 Tons per day | 99.7% |
BDM L-200 | 215 Liters / hr | 6 Tons per day | 99.7% |
BDM L-250 | 290 Liters / hr | 8 Tons per day | 99.7% |
BDM L-300 | 360 Liters / hr | 10 Tons per day | 99.7% |
BDM L-400 | 425 Liters / hr | 12 Tons per day | 99.7% |
BDM L-500 | 540 Liters / hr | 15 Tons per day | 99.7% |
BDM L-1000 | 1170 Liters / hr | 30 Tons per day | 99.7% |
BDM L-1500 | 1755 Liters / hr | 45 Tons per day | 99.7% |
BDM L-2000 | 2340 Liters / hr | 60 Tons per day | 99.7% |
BDM L-3000 | 3515 Liters / hr | 90 Tons per day | 99.7% |
BDM L-4000 | 4685 Liters / hr | 120 Tons per day | 99.7% |
BDM L-5000 | 5850 Liters / hr | 150 Tons per day | 99.7% |
NOTE : THE SAME PLANT CAN ALSO PRODUCE LIQUID NITROGEN ALONG WITH 99.9% PURITY.